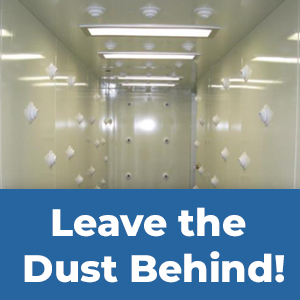
Li-ion batteries have become widespread not only in personal electronics, medical devices, and the aerospace and automotive industries, but also in heavy industrial applications like electric forklifts in the material handling industry, and even mining.
Nevertheless, many industries continue to rely on a lead-acid battery pack, including electric forklifts applications.
Are you using traditional lead acid forklift batteries in your operations? If yes, this article is a must-read! You need to learn what lead decontamination measures are mandated at the place of production (spoiler alert: Pandemic precautions are a joke compared to what you have to do to stop lead poisoning of workers and their families).
Whether you have all the safety protocols in place to prevent lead poisoning and decontaminate before going home to protect your family, the main question is, “Why should you continue using lead?” Dan Askin, a Speaker at a recent BCI event “Worker Decontamination: Preventing Take Home Lead” says it best: “The less lead you start with, the less lead you have to clean up.”
Why Manufacturers of Lead-Acid Batteries Take Workers’ Lead Decontamination Seriously, and Why You Should Too.
On November 4, I participated in a webinar titled “Worker Decontamination: Preventing Take Home Lead & The Role of Operations and Supervisors in Lead Health Programs” organized by Battery Council International. I have full respect for the organizers of this education effort aimed at reducing the harm. I was quite impressed with the mandated lead decontamination measures to prevent spreading lead dust (and consequent lead poisoning) outside of a workplace.
The health risks discussed were mainly those for the families of employees of lead-containing product manufacturers. Today, 75 percent of lead used in industrial manufacturing goes into lead-acid batteries, so we are talking about manufacturers and users of lead-acid batteries here.
Lead Poisoning
Since lead is a dangerous neurotoxin, especially dangerous for children, a safe level of lead dust on the floor is defined at below 10 micrograms (one-millionth of a gram) per square foot. According to Dan Askin, the first speaker at the event and the president and technical director of ESCA Tech, a company developing blood lead level reduction programs, If a worker takes 1 milligram (one-thousandth of a gram) of lead home, that is enough to cover 100 square feet at the U.S. Environmental Protection Agency’s maximum safe level.
Askin provided an example of a one-week test of a battery plant air-shower. At the entry to the men’s locker room, they recovered 108 milligrams of dust per person who walked through the air-shower. This dust was typically 60 to 70 percent lead. That means we are starting with more than 70 milligrams of lead to be removed before a worker leaves the plant. If this much lead from one person was uniformly dispersed throughout the locker room, the result would be 700 square feet of space at 100 micrograms per square foot.
How Can a Worker Take Lead Home?
How can one take lead home? Multiple ways: Lead dust is transmitted on shoes, clothes, skin, hair, fingernails, phones, keys, wallets, coins, tobacco, cosmetics and toiletries, socks, underwear, glasses, watch, rings, jewelry, and of course, cars. It can even be carried in your sweat. To prevent lead from being carried over to homes, companies should install advanced filters in their air conditioning systems throughout the facility, not only in the working areas but also in corridors, meeting rooms, and offices. Enter and exit routes must not cross. A policy of no street clothes or shoes inside must be enforced. If you touch your shoes, re-wash your hands. And wash your car before driving home every day.
Battery manufacturing plants must check daily whether training rooms and chairs are used by people in both street clothes and work clothes. Are the training room chairs cleanable? Where are the socks washed? If the socks are washed at home, lead will collect in the recirculation tank of a home washer and be re-suspended in the rinse water in every load.
And so on. In a nutshell, if your operations involve lead products, the rules of personal protection from lead poisoning and decontamination before you leave the facility to go home must be very strict. And the punishment for not following these rules needs to be quite severe.
When I asked if these measures apply to workplaces that use the lead acid technology, not manufacture them, Askin mentioned battery distribution centers and industrial batteries charging stations, with which they “had issues in the past.” He could not give more details because there is simply not enough data. These facilities are not regulated and measured in the same way as production areas, and the blood lead levels of workers and their families are simply unknown.
Askin finished his presentation with a very clear message: “The less lead you start with, the less lead you have to clean up!”
Testing for lead dust on shoes. Workers’ cars are one of the first lead decontamination targets.
Leave the lead dust behind!
The next two speakers, Carl Raycroft, vice president, EHS compliance, at RSR/ECOBAT, and Pedro Chacon, senior director of manufacturing at Trojan Batteries, both presented examples of policies and best practices at their organizations aimed at mitigating the risk of lead poisoning. Rigorous testing and reporting of the lead blood level test results, investments in lead decontamination equipment and employee education, and hygiene improvements of workplaces, offices, and lunchrooms all lead to reduced lead levels in the blood. And this has also become an important KPI of the management’s performance.
Now, “thanks” to COVID, we all know very well what life in a respirator feels like. And I can truly appreciate the difficulty of this and all the other efforts necessary to keep the risk of lead poisoning at an acceptable level. But listening to the presentations, I kept asking myself, “What is this level of acceptable risk and why do we need to put up with this risk at all?”
In my previous article on some obvious problems with lead-acid batteries recycling called “The New Merchants of Death: Why Lead Acid Batteries Manufacturers Are Increasing Production Volume?” I wrote about the reality of the renowned 99 percent recycling rate of lead-acid batteries. The industry-wide recycling rate was truly a success story of turning something as dangerous as lead to something so acceptable and widespread as lead-acid batteries. With no available commercial alternatives, lead-acid technology was an important achievement, which allowed for economic growth and many engineering inventions. But with readily available, safer, more economical and “greener” power alternatives such as lithium batteries, lead-acid now is simply an outdated technology using a dangerous toxin.
Many companies have already run the numbers and have switched to Li ion batteries to reduce the Total Cost of ownership of material handling equipment in their operations. Others prefer to sub-contract their electric forklifts fleet management to a 3d party, thus not having a choice of the power source. The calculations leading to the use of lead-acid batteries at your workplace probably do not factor in the HSE risks. Because in case you do have all the recommended safety measures in place, like a daily carwash for every car entering the facility, advanced air-filtration, air-showers, automatic footwear cleaners, etc. – your bottom-line would scream for a change of the power source! So the most sensible decision for the users of material handling equipment is to switch to Lithium ion forklift batteries – and leave the lead dust behind, once and for all.