Summary
When it comes to safety and longer cycle life, LFP batteries are superior to NMC and NCA, although their energy density is lower. NMC and NCA both have a considerably higher energy density than LFP, but this article proves that this advantage can only be observed in lab testing. LFP’s performance at the pack level matches that of NMC in terms of specific energy and energy density.
Users of lithium batteries should examine a battery pack’s performance data to make informed decisions.
At the cell level, in both laboratory and real-life performance, NMC cells outperform LFP cells. But the performance data for battery packs show a different picture.
This article is based on the recently published paper «A non-academic perspective on the future of lithium-based batteries,» (Nature Communications, January 2023) This paper provides a comprehensive overview of the significant differences between theoretical and practical performance for the most common lithium technologies.
Figure 1. LFP vs NCA performance in theory, and on cell and pack levels
NMC Performance Decreases 5-fold from Lab to Real-Life Battery Pack
Figure 1 illustrates the decrease in specific energy and energy density of LFP and NCA technologies, from their theoretical potential («Theory») to the practical implementation in an installed device («Pack»). Despite a notable contrast in specific energy (Wh/kg) and energy density (Wh/L) at the cell level, both technologies exhibit similar performance when evaluated at the pack level.
Measurement of performance | Theory | Cell level | Pack level | |||
NMC | LFP | NMC | LFP | NMC | LFP | |
Specific Energy (Wh/kg) | 700 | 350–370 | 250 | 160–180 | 130 | 130–140 |
Energy Density (Wh/l) | 2400 | 1100 | 700 | 330–380 | 250 | 210–230 |
Table 1 NMC vs LFP: theory, cell and pack levels
The data in the table is based on Figure 1, which compares LFP and NCA chemistries. For the purposes of this comparison, the specific energy and energy density of NCA and NMC are assumed to be equal. However, in reality, different sources suggest there may be a 5 to 15% difference between NMC and NCA. The difference in performance between LFP and NMC (or NCA) is significantly greater.
Theoretical calculations suggest that NMC chemistry has at least twice the specific energy and energy density of LFP chemistry. However, on the cell level, NMC only outperforms LFP by a factor of 1.5 on these parameters, and at the pack level, the two chemistries perform similarly.
In practice, the performance of NMC cells is 36% of the theoretical maximum, while pack performance is less than 20% of the theoretical level. On the other hand, the performance of LFP cells is 45–48% of the theoretical level, and pack performance is about 37% of the theoretical level.
Key Reasons for the Significant Differences in Real-Life and Theoretical Performance of Batteries
Battery chemistry research mainly deals with single-cell performance and often overlooks the reduced specific energy and energy density indicators after the cells are assembled into modules or packs. Theoretical research is carried out mostly at levels TRL1–TRL4 of the Technology Readiness Level scale. Academic researchers are generally less familiar with end-user requirements and critical engineering steps toward scalability and industrial batteries production. Batteries are often tested under environmental conditions that differ from those during real-life operations, which is especially true for some power-hungry applications in adverse outdoor and industrial environments.
Another factor is LFP popularity. Battery manufacturers have invested over two decades of engineering into the design of these battery packs, with cell-to-pack (CTP) technology being one of the most effective innovations in assembling industrial battery packs.
Site | Stage | |
Research laboratory | TRL 1 | Idea formulated |
TRL 2 | Proof of concept | |
TRL 3 | Coin cell | |
TRL 4 | Small prototype | |
Pilot plant | TRL 5 | Large prototype, sample with one or more functions or concepts |
TRL 6 | MWh-scale manufacturing, sample with all functions guaranteeing that functions are protected in theory | |
GWh-scale battery manufacturing plant | TRL 7 | EV-grade prototype, automotive part approval |
TRL 8 | GWh-scale manufacturing, vehicle Standard Operating Procedure | |
TRL 9 | System demonstration, production at scale | |
TRL 10 | Widespread adoption, no recall |
Table 2. Technology Readiness Levels
Cell-to-Pack Technology
CTP technology aims to simplify the design and manufacturing of lithium-ion batteries. With this approach, the battery pack is designed as a single unit that integrates multiple cells, thus eliminating the need for interconnects, connectors, and other components required in a conventional cell-to-module battery pack. The CTP approach is a more efficient use of conductive materials (aluminum and copper), cables, and available space inside a battery case.
CTP enables batteries to be designed for specific applications with greater precision and flexibility than is offered by cell-to-module technology, in order to match the pack requirements for voltage and capacity. CTP technology reduces the size, weight, and costs of batteries, especially for large industrial batteries, such as those used in forklifts in the materials handling industry and in other power-hungry operations.
Figure 2. Cell-to-pack technology improves lithium battery performance
Demand Drivers for LFP Lithium Batteries
Longevity and increased safety of the LFP technology. Data on the commercially available cell tests can be found in our article «New Tests Prove: LFP Lithium Batteries Live Longer than NMC.» For example, the flashpoint temperature (when a thermal runaway for a specific chemical is possible) for LFP batteries is significantly higher than for NMC batteries. See Figure 3 for more details about lithium batteries with NMC and LFP cathodes.
LFP battery components are less expensive than NMC components. Nickel and cobalt are expensive and are often associated with unethical mining practices.
Significant improvements in battery performance have followed incremental engineering advancements both on the battery cell level (improvements in electrolyte and membrane materials) and on the pack level with CTP technology.
Mass production of LFP contributed to a sharp decline in battery cell prices, which fell 98% from $5000/kWh in 1991 to $101/kWh in 2021. In 2022, there was a spike in battery metal prices and the price per kWh increased for lithium batteries for the first time in the last decade. This resulted in a sustained preference for less expensive and more reliable LFP batteries over NMC batteries.
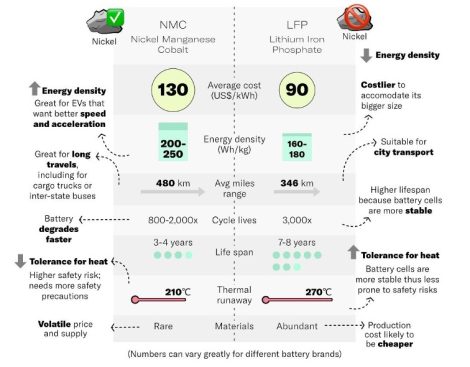
Figure 3. Decoding cathodes (Source: The Ken Research)
Conclusions
Being less expensive and more reliable than NMC batteries, LFP batteries remain the most convenient and affordable technology on the market for many applications, including EVs and off-road electric industrial vehicles.
LFP technology continues to advance on both the cell and pack levels with CTP technology. Furthermore, an improved Battery Management System (BMS) optimizes each cell discharge in real time and provides incremental gains in a battery’s everyday performance, and also extends its cycle life.