Main Lithium Battery Pack Components
Currently, there is no one standardized format for a lithium-ion battery. The battery cell format and shape is selected based on the user’s needs, which ultimately influences the design of the battery module. The current lithium battery market typically offers a three-tier battery concept to customers: cell, module, pack.
The main lithium-ion battery components usually are battery cells, cell contacting, cell fixation, housing, thermal management and the battery management system (BMS), including its periphery. To learn more about cell design, see Types of Lithium Batteries: Lithium Cell Design.
Furthermore, depending on the cathode material composition, the most common lithium-ion cell chemistries are lithium ferric phosphate, or lithium iron phosphate (LFP), lithium nickel manganese cobalt oxide (NMC), and lithium nickel cobalt aluminum oxide (NCA). To learn more about lithium-ion chemistry, see the Types of Lithium Batteries: Lithium Cell Chemistry.
Cell Shapes
Battery cells are designed in different shapes and form-factors: cylindrical, prismatic and pouch cells. The inner structure, the electrode-separator-compound, are different in terms of the dimensions and the manufacturing processes used.
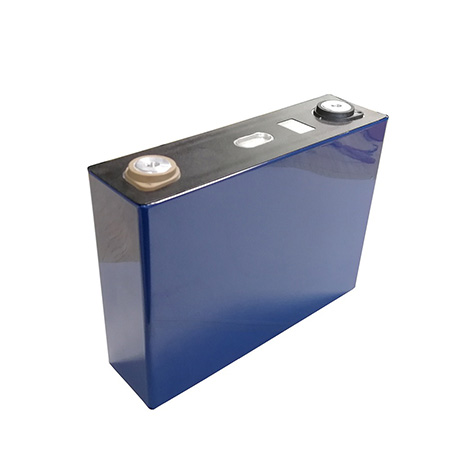
Prismatic lithium cell
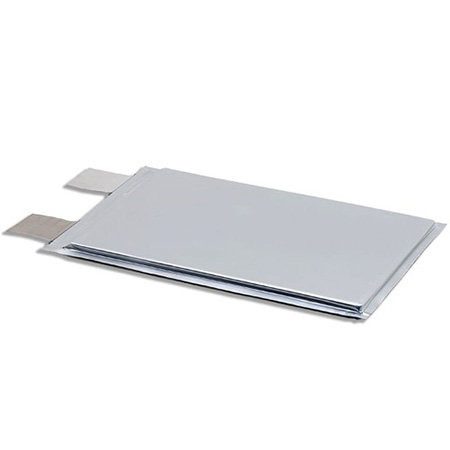
Pouch lithium cell
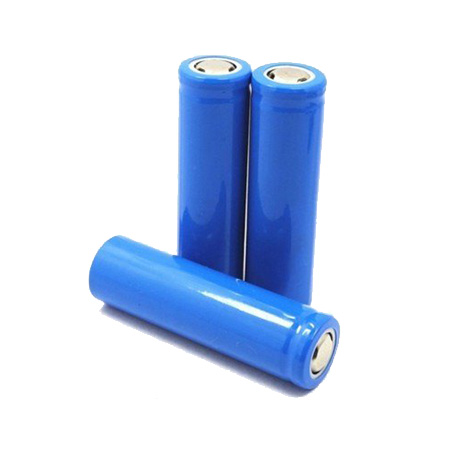
Cylindrical lithium cell
Cylindrical Cells
Cylindrical cells consist of sheet-like battery anode, cathode, and separator that are sandwiched, rolled up, and packed into a cylinder-shaped can. This type of cell is one of the first to be mass-produced and is still very popular. Cells feature multiple rows with the arrester being on opposite sides. They are adhesive connected with busbars by welding technology and are optionally wire bonded. In this case, no support plates are necessary. Cylindrical cells have to be fixated into a battery module or pack by rigid spacers, spacer strips, or mounting brackets. Additionally, glue can be used as the primary fixation of cylindrical cells. These fixings add additional weight and complexity to the battery pack.
Pouch Cells
Pouch cells do not have a rigid outside can and use a sealed flexible foil as the cell container. The electrode and separator layers of a pouch cell are stacked. With pouch cells, the designer should allocate enough space for possible swelling. Modules with pouch cells show single-rowed cells with the arresters being positioned either on the same or the opposite sides. Pouch cells can be connected by adhesive bond welding and in either tab-to-tab or tab-to-busbar bridges without support. Also, they may be connected by a form-fit connection using screws and busbars as a bridge without any support plates.
For pouch cells, cell frames are often used as primary fixation. In this case, the cells are inserted, redundantly sealed and flexibly tensioned. The spaces between the cells could even be additionally used for a cooling system. Optionally, pouch cells may even be glued.
Prismatic Cells
Prismatic cells consist of large sheets of anodes, cathodes, and separators sandwiched, rolled up, and pressed to fit into a metallic or hard-plastic housing in cubic form. The electrodes can also be assembled by layer stacking. Lithium prismatic cells feature either single-row or two-row modules and the arresters are always on the same side regardless of the row.
Prismatic cells are either adhesive-bonded by welding, with busbars and support plates or traction / form-fit connected with screwing/] or latching as joining technology and hole-busbars as a bridge. Lastly, prismatic cells can be fixed by gluing. This requires a light and elastic joining medium to avoid air pockets.
Technical Comparison
Cylindrical cells are usually produced in standard models in terms of size. One common size is the 18650 type (18 mm diameter, 65 mm height). This type has a total mass of about 45 grams and can support a capacity of about 1.2 to 3 Ah depending on the technology employed.
Pouch cells have a soft construction that requires the use of a support structure with these cells. Additionally, the cell should not be placed near sharp edges. The approximate cell capacity range is 2.5-8 Ah, and the approximate weight is 75-225 g.
Prismatic cells are manufactured with a capacity ranging from several Ah targeted for laptops and cell phones to hundreds of Ah designed for EV applications. The weight range is 0.8-5.2 kg.
Comparison of Cylindrical, Pouch and Prismatic Battery Cells
Advantage | Disadvantage | |
Cylindrical cell |
|
|
Pouch cell |
|
|
Prismatic cell |
|
|
Applications
Cylindrical cells are widely used in power tools, toys, lamps, the automotive industry, e-bikes and some portable mobile energy systems.
Pouch cells are widespread in smartphones, drones, laptops, wearable devices, etc.
Finally, prismatic cells are widely used in electric vehicles, including off-highway industrial trucks and different types of forklifts, communication-based stations, grid energy storage, medical fields, etc.
Prismatic Cells are the Best Choice for Forklift Batteries
The differences in battery technology today allow customers to choose the best fit for their applications. Thus, lithium prismatic cells are the preferred technology for material handling equipment (MHE):
Hundreds of Ah nominal capacity. The technology provides the best ratio of power and energy per volume unit. This is especially important in the high-capacity, high-current and relatively low voltage batteries used in MHE.
Optimal utilization of available pack space. There are no space cavities between the cells. This allows maximum capacity for the battery pack, and still have enough room to accommodate for required extra weight, sealing, heater, internal charger or other battery upgrades within the battery compartment’s limited area.
Contacts are strong enough for reliable bus-bars connection. This is a hugely important safety factor with high vibration operations, especially in cushion-tire type lift trucks.
Flexible battery weight. LIB pack weight is not a limitation for most of the MHE in terms of its range per one charging (unlike passenger EVs). Forklifts operate mostly near their charging stations and their batteries are often engineered as a counterweight.